-
Klimaschonende Sozialwohnungen mit Geopolymerbeton
Beim Bau von 71 Sozialwohnungen im Rahmen des Projekts 4HÖFE kommt klimafreundlicher Geopolymerbeton der MC zum Einsatz.
Geopolymerbeton für klimaschonenden Wohnungsbau
Deutschland
In Norderstedt werden im Rahmen des Projekts UBS4 71 klimaschonende Sozialwohnungen gebaut. Die Gebäude werden in Holzskelettbauweise auf Geopolymerbeton errichtet – eine Bauweise, die das Projekt im Norden Deutschlands zu einem landesweiten Vorzeigeobjekt macht.
-
Name
Geopolymerbeton für klimaschonenden Wohnungsbau
-
Land
Deutschland, 2023
-
Fields of Expertise
-
Kategorie
-
Produkte
Das Neubauprojekt 4HÖFE ist eines der größten und wichtigsten Bauvorhaben Norderstedts. Im Zentrum der Stadt entstehen auf vier Baufeldern rund 300 Wohnungen, darunter Eigentums-, Miet- und Seniorenwohnungen. Verantwortlich für die Entwicklung der Grundstücke ist das Kellinghusener Unternehmen Behrendt & Struck Wohnwerte.
71 klimaschonende Sozialwohnungen
Auf einem der vier Baufelder geht ein besonderes Pilotprojekt an den Start. Die Firma blu – Gesellschaft für nachhaltige Immobilienprojekte mbH, Tochter der Hamburger AUG. PRIEN Bauunternehmung (GmbH & Co. KG), baut dort, als späterer Eigentümer und Vermieter, unter dem Projektnamen UBS4 71 klimaschonende Sozialwohnungen. Auf 4000 m² sollen drei vier- bis fünfgeschossige Gebäude entstehen, eins an der Ulzburger Straße und zwei an der Bahnlinie. Zusätzlich wird das Quartier mit einer Tiefgarage ausgestattet, die Platz für 40 Autos, 142 Fahrräder und 71 Abstellräume bietet. Alle Wohnungen zwischen 50 und 100 m² Grundfläche werden mit der gleichen Bad- und Küchenausstattung versehen. Auch die Außengestaltung überzeugt: Alle Häuser erhalten eine selbsttragende Verblend-Fassade in Rotklinker–Optik sowie Vorstellbalkone aus Stahl.
Nachhaltige Energieversorgung
Mit dem Bauvorhaben möchte blu herausfinden, wie viel CO2 im geförderten Wohnungsbau eingespart werden kann. Um die Gebäude so nachhaltig wie aktuell möglich zu errichten, setzt das Projektteam auf verschiedene umweltschonende Maßnahmen. So werden, im Gegensatz zu den anderen Wohnungsanlagen im Projekt 4HÖFE, Strom und Wärme über Photovoltaikanlagen auf dem Dach und eine große Wärmepumpe bezogen. Die Fassaden der drei Häuser im Bauvorhaben UBS4 werden aus Recycling-Klinker bestehen, als Dämmung wird umweltfreundliche Zellulose eingesetzt. Außerdem sind viele der Bauelemente standardisiert und werden fertig angeliefert. Besonders auffallend ist jedoch die Bauweise der drei Häuser: Auf einem Stahlbetonsockel aus Geopolymerbeton wird in Holzskelettbauweise die Tragstruktur der Gebäude errichtet.
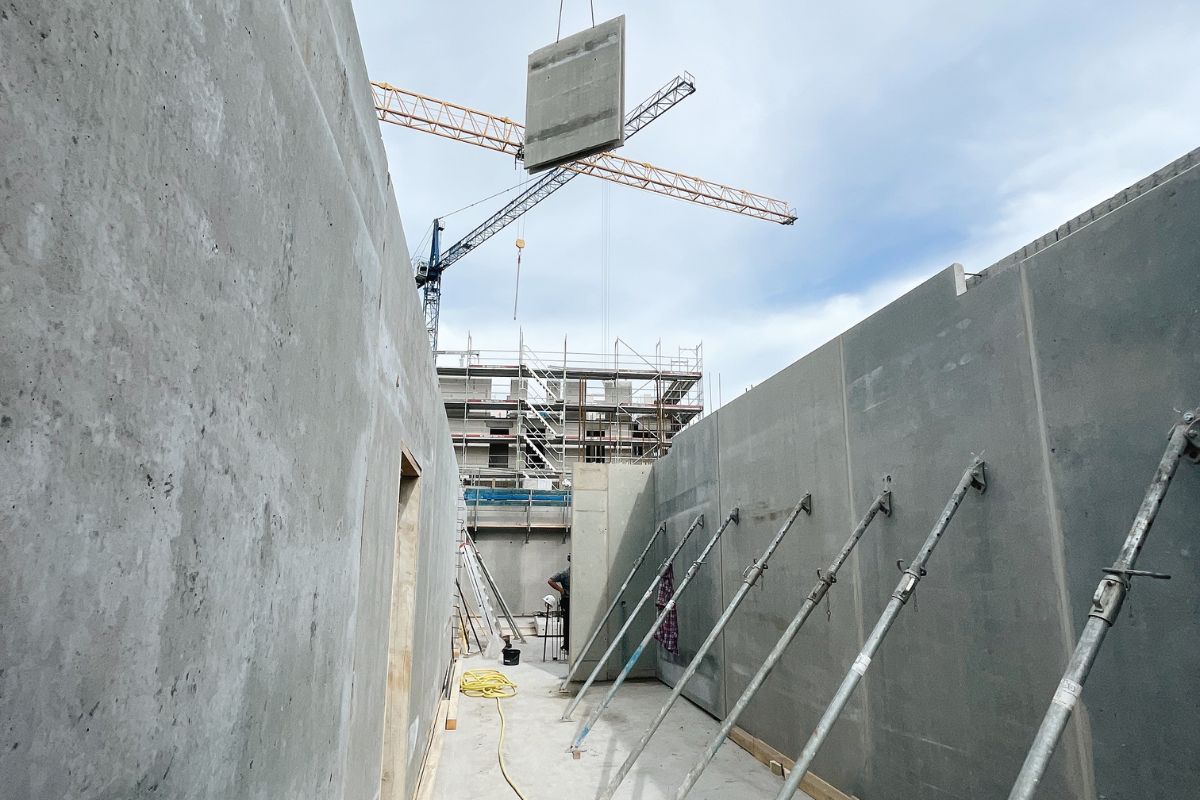
© blu – Gesellschaft für nachhaltige Immobilienprojekte mbH 2025
Nachhaltiges Bauen
Geopolymerbeton ist eine umweltfreundliche Alternative zu herkömmlichen, zementösen Beton. Er enthält Bindemittel auf Basis industrieller Nebenprodukte wie Hüttensand oder Flugasche, die hier von Holcim Deutschland geliefert werden. Der internationale Entwickler und Hersteller bauchemischer Produkte MC-Bauchemie aus Bottrop forscht kontinuierlich an nachhaltigen Lösungen für die Beton- und Bauindustrie. Zusammen mit dem australischen Unternehmen Wagners hat MC-Bauchemie den ersten zementfreien Beton, den sogenannten Earth Friendly Concrete (EFC), entwickelt. Die erforderliche DIBt-Zulassung für den Beton wurde erstmalig im September 2019 erteilt. Daher setzten die Auftraggeber der Firma blu bei der Entwicklung der klimaschonenden Wohnungen auf das umfassende Fachwissen der MC. Im Vergleich zu Referenzbetonen auf der Bindemittelbasis Zement, ermöglicht der EFC eine CO2-Ersparnis von bis zu 75 %. Dies belegt auch das Global Warming Potential (GWP), welches in der Life Cycle Analysis (LCA) der KIWA ermittelt wurde.
Bauen mit Geopolymerbeton
Um das Bindemittel zur Herstellung des zementfreien Betons zu aktivieren, wurde ein pulverförmiger DIBt-zugelassener Aktivatoren Compound der MC eingesetzt. Die Mischeinheit und die Gebindegröße wurden dabei so angepasst, dass immer die richtige Menge Wasser und Aktivatoren für 6 m3 Geopolymerbeton zusammengeführt werden. Es wurden zwei Mischeinheiten verwendet, die parallel jeweils das Material für 6 m³ bevorraten. Dadurch können mindestens fünf Betonansätze die Stunde hergestellt und eine Produktivität von 30 m³ pro Stunde sichergestellt werden. Um die Verarbeitungsdauer von 90 Minuten einzuhalten, kam das Hochleistungsfließmittel MC-PowerFlow 4100 der MC zum Einsatz. Mit diesem konnten die Verarbeitungseigenschaften sowohl für die Fertigteile, hier vom Elementhersteller fdu GmbH & Co. KG, als auch für den Transportbeton, der im Zusammenspiel zwischen Betonlift GmbH & Co. KG und Betonlabor Süderelbe GmbH &Co. KG gefertigt wurde, zielgenau eingestellt werden.
Modellvorhaben mit Zukunft
Die Bauarbeiten im Projekt UBS4 haben im Juli 2023 begonnen. Schon im Oktober 2024 sollen die Wohnungen bezugsfertig sein. “Wir freuen uns sehr, dass wir mit diesem Bauvorhaben einen Beitrag hin zum klimagerechten Bauen leisten können. Das Projekt zeigt, was in der Baubranche möglich ist, wenn sich viele Akteure auf ein gemeinsames Ziel verständigen und Ihre Kompetenzen bündeln“, so Carsten Joost, Geschäftsführer der blu. Mit seiner einzigartigen Bauweise mit Geopolymerbeton ist UBS4 ein wahres Zukunftsprojekt, das nicht ohne Grund vom Land Schleswig-Holstein zu einem landesweiten Modellvorhaben ernannt wurde.
ÄHNLICHE INHALTE
-
News
Klicken Sie hier, um zu unseren News zu gelangen.
-
MC-Pedia
In unserer MC-Pedia finden Sie fachliche Artikel zu unterschiedlichen Themen, die exklusiv von unseren Spezialisten geschrieben wurden.
-
Magazine
Klicken Sie hier, um zu den aktuellen Ausgaben unseres Kunden- und Mitarbeitermagazins MC aktiv zu gelangen.
-
Downloads
Hier finden Sie alle relevanten Datenblätter unserer Produkte sowie Broschüren unseres Unternehmens sowie unserer Fachgebiete und Produktkategorien.
-
Referenzen
Klicken Sie hier, um zu unseren aktuellen Referenzen und Projektberichten zu gelangen.
-
Karriere
Klicken Sie hier, um zum MC-Karrierebereich zu gelangen.
-
Kontakt
Klicken Sie hier, um zu unserer Kontaktseite zu gelangen.