wir Ihnen helfen?
-
Nachhaltigkeit
MC forscht für nachhaltiges Bauen
Schon seit Jahren ist der Zement ein großes Problem beim Thema Nachhaltigkeit in der Baubranche. Daher soll künftig die Entwicklung zementfreier Baustoffe dazu beitragen, die Klimabilanz der gesamten Branche deutlich zu verbessern. MC forscht in diesem Bereich ganz vorne mit und entwickelt mit neuen Technologien und nachhaltigen Lösungen schon heute die Standards von morgen.
Zementfrei in die Zukunft
14.10.2024
Das Thema Nachhaltigkeit spielt in der Baubranche seit Jahren eine zentrale Rolle – und damit rückt vor allem der Zement aufgrund seiner problematischen CO2-Bilanz immer stärker in den Fokus. Die Entwicklung zementfreier Baustoffe soll künftig dazu beitragen, die Klimabilanz der gesamten Branche deutlich zu verbessern.
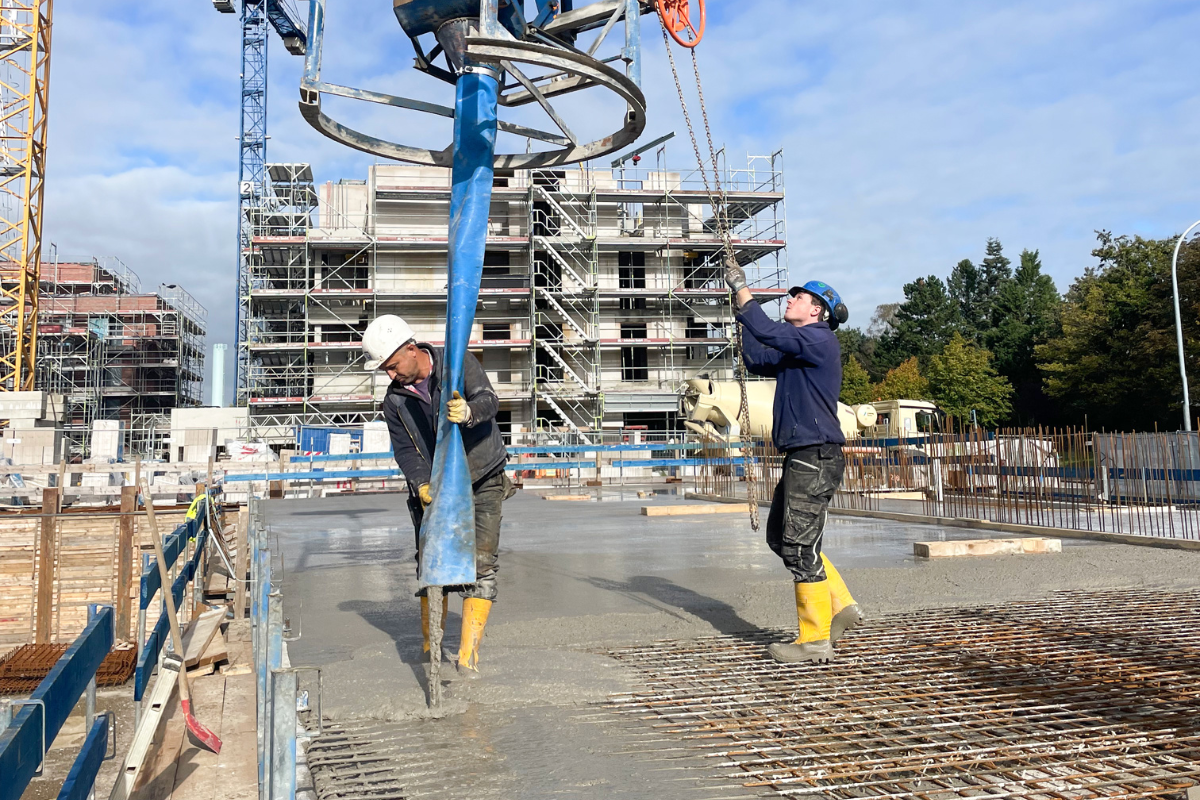
© blu – Gesellschaft für nachhaltige Immobilienprojekte mbH
Ohne Beton geht beim Bau nichts: Rund 14 Milliarden Kubikmeter Beton werden jährlich weltweit verbaut. Dafür wird Zement benötigt. Doch dessen Herstellung ist nicht nur enorm energieaufwändig, sondern verursacht auch große Mengen an CO2. Im Jahr 2023 wurden weltweit geschätzte 4,1 Milliarden Tonnen Zement produziert. Dabei setzte die Zementproduktion knapp drei Milliarden Tonnen CO2 frei - und damit aktuell rund acht Prozent der gesamten von Menschen verursachten Emissionen an Kohlenstoffdioxid. Bei Transportbeton beansprucht Zement mit 85-90 % den Hauptanteil der für die Produktion notwendigen Energie. Ebenso wird das Treibhauspotential des Betons zu 95 % durch die mit der Zementherstellung verbundenen CO2-Emissionen dominiert. Um die Pariser Klimaziele der Europäischen Union und damit Klimaneutralität bis 2050 zu erreichen, muss der Bausektor seine Emissionen in den kommenden zwei Jahrzehnten drastisch senken. Diese Mammutaufgabe ist ohne zementfreie Betone nicht zu bewältigen. In diesem Zusammenhang setzen auch die Bauherren immer mehr auf nachhaltiges Bauen und streben eine bestmögliche DGNB-Zertifizierung ihrer Bauwerke an. Insbesondere große Unternehmen und Kommunen verstärken ihre Bemühungen, CO2 einzusparen. Dementsprechend wächst das Interesse an zementfreien Betonen kontinuierlich – und das europaweit.
Der Weg zur grünen Null: Zementfreie Betone
Seit mehr als 100 Jahren wird bereits an alkalisch aktivierten Bindemittelsystemen als Zementersatz geforscht. Seit den 1970er Jahren wurde dabei die Forschung an Geopolymeren als Zuschlagstoffen intensiviert. Doch ein echter Durchbruch gelang erst in jüngster Zeit dem australischen Unternehmen Wagners mit EFC® (Earth Friendly Concrete®), einem geopolymeren Bindemittel, das auf Industrieabfällen wie Hochofenschlacke und Flugasche basiert. EFC® enthält keinen Zement und verursacht dadurch deutlich weniger CO2-Emissionen. Stattdessen kommen beispielsweise Hüttensand aus der Roheisen-Produktion oder Klinker-Ersatzstoffe wie gebrannter Ölschiefer zum Einsatz. Hinzugefügt werden spezielle Aktivatoren und Betonzusatzmittel, die von der MC kommen und auf die individuelle Anwendung abgestimmt werden. Bei Earth Friendly Concrete handelt es sich allerdings keinesfalls um einen „Betonersatz“ – sondern vielmehr um einen neuen Baustoff mit einer Reihe spezifischer Vorteile. Der Verzicht auf Zement in der Betonmischung bedeutet eine reduzierte Menge an Kalzium und somit weniger Reaktivität mit anderen Stoffen. Dies führt zu einem widerstandsfähigeren Beton, besonders gegenüber chemischen Angriffen und Säure (Expositionsklasse XA3). Damit entfällt in der Regel die zusätzliche Beschichtung bzw. die Auskleidung von Bauteilen. Darüber hinaus hat zementfreier Beton einen bis zu 75 % geringeren CO2-Fußabdruck im Vergleich zu konventionellem Beton.
MC-Bauchemie leistet Pionierarbeit
Bereits bei der Produktreife des EFC® von Wagners war MC maßgeblich involviert. Die Abteilung Forschung & Entwicklung der MC arbeitete an der Betonrezeptur mit und entwickelte spezielle Aktivatoren und Fließmittel, um die für einen effizienten EFC-Einbau erforderlichen Anwendungseigenschaften zu erreichen. Die daraus entstandene Geopolymerbetonmischung ist schlussendlich auch das Ergebnis von zehn Jahren Entwicklungsarbeit bei MC. Bei einem ersten Großprojekt 2014 wurde bei der Erweiterung des Flughafens Brisbane Westwellcamp EFC®-Beton sowohl für 51.000 m² Schwerlastbeläge für Wendeknoten und Rollbahnbereiche als auch für die Fundamente und Wandplatten des Terminalgebäudes geliefert. Allein bei diesem Projekt wurden rund 8.800 Tonnen CO₂-Emissionen durch die Verwendung von EFC® eingespart.
EFC mit DIBt-Zulassung
Der erste Compound für EFC® aus deutscher Produktion, zugelassen für Transportbeton und Fertigteile mit der DIBt-Zulassung Z-3.15-2157, kommt von der Holcim Deutschland GmbH. Auch hier spielte MC eine wichtige Rolle, denn die Verbindung aus Sekundärrohstoffen wie Schlacken oder Aschen, die in anderen Industriezweigen als mineralische Nebenprodukte entstehen, kann erst durch den von Wagners und MC entwickelten Aktivator den Zement ersetzen. Damit nicht genug, wurde mit MC-PowerFlow 4100 in den Laboren der MC in Bottrop eine Hochleistungsfließmittelserie entwickelt, die sich optimal für die Verwendung in Geopolymerbeton eignet. Sie wurde speziell für Bindemittelkombinationen aus gemahlener granulierter Hochofenschlacke und Flugasche zugelassen und bewirkt eine starke Verflüssigung bei wirtschaftlicher Dosierung. Der spezifische Funktionsmechanismus ermöglicht die Herstellung von zementarmen und zementfreien Hochleistungsbetonen ohne Erhöhung der Klebekraft mit hervorragenden Verarbeitungseigenschaften und ohne Entmischungs- und Ausbluteffekte.
Großprojekt mit MC-PowerFlow 4100
Im großen Stil kam Earth Friendly Concrete zwischen 2023 und 2024 in Norderstedt beim Neubauprojekt 4HÖFE zum Einsatz. Im Zentrum der Stadt entstanden auf vier Baufeldern rund 300 Wohnungen, darunter Eigentums-, Miet- und Seniorenwohnungen. Um mögliche Potenziale bei der Einsparung von CO2 im sozialen Wohnungsbau genauer zu untersuchen, ließ die blu – Gesellschaft für nachhaltige Immobilienprojekte mbH, eine Tochter der Hamburger AUG. PRIEN Bauunternehmung (GmbH & Co. KG), auf einem der vier Baufelder 71 klimaschonende Sozialwohnungen in Holzskelettbauweise auf Geopolymerbeton errichten – eine Bauweise, die das Projekt deutschlandweit zu einem Vorzeigeobjekt macht (wir berichteten in der MC aktiv 3/23). Auch hier war für den zementfreien Beton das Hochleistungsfließmittel MC-PowerFlow 4100 die erste Wahl, um die Verarbeitungseigenschaften sowohl für die Fertigteile vom Elementhersteller fdu GmbH & Co. KG als auch für den Transportbeton, der im Zusammenspiel zwischen Betonlift GmbH & Co. KG und Betonlabor Süderelbe GmbH &Co. KG gefertigt wurde, zielgenau einstellen zu können. Das Ergebnis beeindruckte nicht nur den Bauherren: Im Vergleich zu Referenzbetonen auf der Bindemittelbasis Zement, ermöglichte der EFC eine CO2-Ersparnis von bis zu 75 %. Dies belegt auch das Global Warming Potential (GWP), das in der Life Cycle Analysis (LCA) der KIWA ermittelt wurde.
Kanalsystem aus next.beton
Die Entwicklung zementfreier Betone macht sich auch die Zementrohr- u. Betonwerke Karl Röser & Sohn GmbH zunutze. Mit next.beton bringt das Unternehmen aus Mundelsheim nach eigener Aussage gerade „Deutschlands klimafreundlichstes Kanalsystem“ auf den Markt. Die next.beton Rohre werden statt aus herkömmlichem Beton aus einem zementfreien Geopolymerbeton gefertigt. Auch hier konnte MC-Bauchemie die Produktentwicklung und Produktoptimierung erfolgreich unterstützen. Die zementfreie Betontechnologie bietet nicht nur ein erhebliches CO2-Einsparpotenzial von bis zu 75%, sie schont auch primäre Rohstoffe - ohne jede Beeinträchtigung der technischen und konstruktiven Qualitäten des Betons. Im Gegenteil: Die Rohre aus next.beton zeichnen sich durch einen hohen Widerstand gegen Säure- und Sulfatangriffe aus, dabei entspricht der Beton der Expositionsklasse XA3 und kann ohne die sonst erforderlichen zusätzlichen Schutzmaßnahmen eingesetzt werden.
Häuser aus dem Drucker
Einen Schritt in die Zukunft des Bauens erleben wir derzeit mit dem 3D-Druck mit Beton. Statt Stein auf Stein gebaut, wird ein Haus mit einem 3D-Drucker erstellt. Die Häuser sehen mit ihrem teils futuristischen Touch nicht nur gut aus, sie sind auch äußerst günstig und schnell errichtet. Die Technik steht derzeit wie kaum ein anderes Verfahren für Fortschritt am Bau. In Deutschland ging man noch einen Schritt weiter: Im westfälischen Beckum entstand das erste Tiny House aus dem Drucker aus zementfreiem Beton – mit MC-PowerPrint GeCO2, einem Mörtel auf zementfreier Bindemittelbasis für den 3D-Betondruck.
3D-Druck mit EFC
Das Planungsbüro MENSE-KORTE aus dem Münsterland und die auf 3D-gedruckte Fertigteile spezialisierte Röser GmbH aus Laupheim setzten dieses richtungsweisende Bauvorhaben zusammen mit der MC um. Die Experten der MC mussten dafür in kürzester Zeit ein Produkt entwickeln, das die statisch erforderlichen Eigenschaften sowie das für den 3D-Betondruck notwendige Verarbeitungsverhalten bietet und gleichzeitig die CO₂-Emissionen signifikant reduziert. Das Ergebnis nach nur einem Jahr: MC-PowerPrint GeCO2, ein Mörtel für den 3D-Druck. Da bei MC-PowerPrint GeCO₂ alternativ zum Zement auch ein additiviertes System aus Hüttensand und Flugasche eingesetzt werden kann, können auch hier im Vergleich zu zementösen Mörtelprodukten bis zu 70% der CO₂-Emissionen eingespart werden.
MC-PowerPrint GeCO₂ bietet eine für diese Technik ideale Thixotropie, das heißt, der Mörtel ist unter Einwirkung von Energie, beispielsweise beim Pumpen durch den Drucker, verflüssigt und damit leicht pumpbar und verformbar, wird jedoch nach Ende dieser Einwirkung standfest. Damit entsteht auch nach mehreren Drucklagen ein schönes und gleichmäßiges Druckbild ohne Verformung durch das Eigengewicht.
Forschung und Entwicklung bei MC
Dem Thema Nachhaltigkeit sowie der CO₂-Bilanz in der Baubranche wird mit zunehmendem Druck auf die Gesellschaft, die Klimaziele von Paris zu erreichen, eine immer größere Bedeutung zukommen. Es gilt daher, richtungsweisende Lösungen zu entwickeln, um einerseits die vorhandenen Ressourcen besser zu nutzen und andererseits den Energieverbrauch für die Herstellung essenzieller Baustoffe weiter zu reduzieren. Unter der Leitung von John van Diemen, Bereichsleiter Forschung & Entwicklung, wird bei MC die Entwicklung zementfreier Alternativprodukte im Bausektor in mehreren Bereichen vorangetrieben. Zum Expertenteam gehören der Laborleiter für mineralische Baustoffe Dr. Karsten Koppe mit seinem Team um Chemiker Dr. Max-Fabian Volhard und Chemietechniker Anton Martin für das Segment; außerdem Florian Beyer-Wittkamp als Laborleiter Polymer Synthesis für den Bereich Zusatzmittel für zementfreie Betone, Diplom-Mineraloge Eugen Kleen und Laborspezialist Dirk Uhlmann im Bereich Tunneling sowie Kai Markiefka als Product Line Manager und Julian Fleige in der Anwendungstechnik. Mit Dr.-Ing. Stephan Uebachs von Brahmeshuber + Uebachs beratende Ingenieure für Baustofftechnologie aus Aachen verbindet MC eine langjährige Zusammenarbeit. Brahmeshuber + Uebachs begleitet die institutionellen Messungen und Zulassungen seit Beginn der EFC-Entwicklung.
Zementfrei nicht nur im Beton
Die Experten der MC arbeiten daran, neue Technologien und nachhaltige Lösungen zu kombinieren, um den Zementverbrauch in so vielen Bereichen wie möglich reduzieren oder sogar ganz vermeiden zu können. Hier reicht das Portfolio der MC von zementfreien Spezialanwendungen wie Ringspaltmörtel im Tunnelbau oder Oberflächenschutzsystemen über Systeme für die Bauwerksabdichtung und den weltweit ersten zementfreien Feuchteregulierungsputz bis zu „alltäglichen“ Bauprodukten wie zementfreien Mörteln oder grünen Systemen für den Bodenaufbau. Letztere werden von Botament, einer Schwesterfirma der MC, unter dem Markennamen BotaGreen bereits erfolgreich vermarktet. Das belegt die Auszeichnung aller BotaGreen-Produkte mit EC1PLUS, dem höchstmöglichen EMICODE®-Siegel bei der Produktklassifizierung für emissionsarme Verlegewerkstoffe und Bauprodukte.
Blickrichtung Zukunft
Weitere Projekte stehen in den Startlöchern, die bereits in nächster Zukunft aus dem Baustellenalltag nicht mehr wegzudenken sein werden. Dazu zählen Pflaster- sowie Dachsteine, für die MC eine funktionsfähige, erdfeuchte, zementfreie Rezeptur für den Kernbeton entwickelte. Auch bei diesen Steinen bieten die alkalisch aktivierten Baustoffe einen echten Mehrwert: Sie erreichen eine höhere Festigkeit als Beton, sind widerstandsfähiger und neigen im Gegensatz zu herkömmlichen Pflaster- und Dachsteinen nicht zu Ausblühungen.
Fazit
Die vorgestellten Innovationen und Lösungen zeigen, dass für Baustoffe die Auswahl an zementfreien Alternativen immer vielfältiger wird. Dabei wird zudem mehr und mehr deutlich: Im Bereich des Bauwesens können wichtige Beiträge geleistet werden, um die Klimabilanz der gesamten Branche deutlich zu verbessern und so einen Teil zur Zukunftssicherung der Menschheit beizutragen. Egal ob Earth Friendly Concrete, Geopolymer, 3D-Druck oder der Ersatz von Zement in weiteren Baustoffen: die kontinuierliche Forschung & Entwicklung der MC trägt dazu bei, den steigenden Anforderungen der Bauwirtschaft gerecht zu werden und gleichzeitig innovative und nachhaltige Lösungen anzubieten. Mit zementfreien Produkten sowie der fachlichen Unterstützung durch erfahrene Experten und Berater nimmt die MC eine führende Rolle im Bereich nachhaltiger Baustoffe ein – und entwickelt heute bereits die Standards von morgen.
Ähnliche Produkte
ÄHNLICHE INHALTE
-
News
Klicken Sie hier, um zu unseren News zu gelangen.
-
MC-Pedia
In unserer MC-Pedia finden Sie fachliche Artikel zu unterschiedlichen Themen, die exklusiv von unseren Spezialisten geschrieben wurden.
-
Magazine
Klicken Sie hier, um zu den aktuellen Ausgaben unseres Kunden- und Mitarbeitermagazins MC aktiv zu gelangen.
-
Downloads
Hier finden Sie alle relevanten Datenblätter unserer Produkte sowie Broschüren unseres Unternehmens sowie unserer Fachgebiete und Produktkategorien.
-
Referenzen
Klicken Sie hier, um zu unseren aktuellen Referenzen und Projektberichten zu gelangen.
-
Karriere
Klicken Sie hier, um zum MC-Karrierebereich zu gelangen.
-
Kontakt
Klicken Sie hier, um zu unserer Kontaktseite zu gelangen.