wir Ihnen helfen?
-
3D-Betondruck
Schöne neue Welt des Bauens
Es gibt eine Reihe von aktuellen Forschungsprojekten rund um den 3D-Betondruck, bei dem das betontechnologische Know-how der MC immer wieder gefragt ist.
3D-Betondruck
12.11.2018
Noch zu Beginn dieses Jahrzehnts wirkte der 3D-Druck wie eine recht abenteuerliche Melange aus Science Fiction und Nischentechnologie für wenige ausgewählte Unternehmen weltweit. Doch das hat sich dramatisch gewandelt. Derzeit werden immer wieder neue Anwendungsmöglichkeiten ins Spiel gebracht. Dabei ist ein Bereich ganz besonders spannend: der 3D-Betondruck, mit dem sich sehr individuelle Bauteile ebenso realisieren lassen wie ganze Gebäude. Bei aktuellen Forschungsprojekten ist das betontechnologische Know-how der MC immer wieder gefragt.
Das gedruckte Haus
Häuser aus dem Drucker? Was im ersten Moment noch recht befremdlich klingen mag, ist in der Baubranche eines der großen Technologiethemen von Morgen. Dabei sind Experten, Planer und Unternehmen weltweit auf der Suche nach neuen Konzepten, mit denen man schnell, umweltverträglich und soweit wie möglich kostengünstig bauen kann. Das gilt für die ausufernden Metropolen der Industrienationen ebenso wie für die geradezu explodierenden Megastädte der Entwicklungs- und Schwellenländer.
In den USA, Großbritannien, China und nicht zuletzt in Deutschland wurden Projekte zur Forschung und Entwicklung eines serienreifen, für die Massenproduktion geeigneten Verfahrens des 3D-Betondrucks vorangebracht. Im Rahmen des Forschungsprojekts „Beton-3D-Druck“ aus dem Förderprogramm „ZukunftBau“ des Bundesinstituts für Bau-, Stadt- und Raumforschung sollen beispielsweise die Grundlagen zur Einführung eines neuen Bauverfahrens untersucht werden. Dabei ist auch die Expertise der MC gefragt: Deren Spezialisten bringen in aktuellen Forschungsprojekten ihr betontechnologisches Know-how und ihre fachmännische Begleitung in Verbindung mit innovativen Betonzusatzmitteln wie z. B. Erhärtungsbeschleunigern sowie faserverstärktem Mörtel mit ein.
Drei verschiedene Ansätze beherrschen derzeit die Diskussion um die Fertigung von Strukturen und Teilen im 3D-Betondruck: die Pulverbetttechnik, die aktuell weiter verbreitete Extrusionstechnik sowie das Nassspritzverfahren.
Die Pulverbetttechnik
Die Pulverbetttechnik lässt sich in zwei unterschiedlichen Ansätzen verfolgen: Entweder wird ein Gesteinskörnungsgemisch durch lokales Auftragen von Zementleim zu einem Komposit verbunden oder eine Verfestigung wird durch punktuelles Auftragen von Wasser auf ein Gemisch aus Gesteinskörnung und Zement erreicht. Bei beiden Techniken können selbst filigrane Strukturen problemlos erzeugt werden – doch gerade bei größeren Bauteilen sind zahlreiche Arbeitsdurchgänge notwendig, so- dass die Prozessgeschwindigkeit relativ gering ausfällt.
Die Extrusionstechnik
In der Extrusionstechnik legt ein Düsenkopf Materialstränge unterschiedlicher Form, Höhe und Breite schichtweise aufeinander ab. Man spricht daher auch von einem additiven Verfahren. Der Prozess ist am ehesten mit dem etablierten konventionellen 3D-Druck mit Kunststoffmaterialien zu vergleichen. Das Verfahren ist zwar schneller, hat aber ebenfalls eine Schwachstelle – und das im wahrsten Wortsinn.
Da die Materialstränge einzeln aufeinander „abgelegt“ werden, ergibt sich der Haftungsverbund nur durch das Anpressen des jeweils neuen Stranges an den darunter liegenden. Hier kann es daher zu Problemen bei mechanischer Belastung hinsichtlich der Biegezug- bzw. Scherfestigkeit kommen.
Das Nassspritzverfahren
Das Nassspritzverfahren ist ebenfalls ein additives Verfahren und ähnelt der Extrusionstechnik. Auch hier wird das vorgemischte Nassspritzgut zu einer Spritzdüse gepumpt, dort unter Druckluftzufuhr beschleunigt und Schicht auf Schicht auf dem Untergrund appliziert. Aufgrund der hohen Auftragsrate und der hohen Prozessgeschwindigkeit eignet sich das Verfahren sehr gut für die Fertigung großformatiger, räumlicher Bauteile. Der Einsatz des Betonspritzverfahrens ermöglicht es, im Gegensatz zum Extrusionsverfahren, den Auftragswinkel der Spritzdüse vertikal und horizontal zu variieren. Dies führt zu neuen Möglichkeiten im Hinblick auf die erzeugbaren geometrischen Formen. Filigranere Strukturen sind dabei jedoch kaum zu erzielen. Außerdem bringt der größte Vorteil des Verfahrens auch eine Herausforderung mit sich: Der hohe Druck beim Auftrag sorgt einerseits für eine außerordentlich hohe Verdichtung des Materials – doch werden dadurch auch vermehrt Rückstände freigesetzt, mit denen in Form von Staub- und Aerosolentwicklung umgegangen werden muss. Alle drei genannten Techniken haben also ihre Stärken und Schwächen. Grund genug für zwei deutsche Forschungsprojekte, sich intensiver mit der Verfahrens-optimierung im 3D-Betondruck zu beschäftigen.
Forschung an der TU Braunschweig
Unter Leitung des ITE, dem Institut für Tragwerksentwurf der TU Braunschweig, befasste sich eine interdisziplinäre Forschergruppe unter Beteiligung der TU Braunschweig, der TU Clausthal und der LU Hannover mit der Entwicklung einer robotergesteuerten Spritzbetontechnologie zur schalungslosen Herstellung komplexer Betonbauteile. Dabei stellte man bereits zu Beginn der Forschungen fest, dass im Vergleich zu vielen anderen Fertigungsbereichen, in denen die digital gestützte Produktion bereits weit vorangeschritten ist, in der Herstellung von Betonfertigteilen bislang vor allem Techniken zum Einsatz kommen, die seit Jahrzehnten am Markt etabliert sind. Damit wurde viel Potenzial verspielt – einerseits im Hinblick auf die kreativen und konstruktiven Möglichkeiten, nicht zuletzt aber auch in wirtschaftlicher Hinsicht. Die neue Fertigungstechnik eröffnet Architekten die Realisierung völlig individuell gestalteter, geometrisch komplexer Betonbauteile und somit neue kreative Möglichkeiten, die mit den bestehenden Techniken nicht möglich sind. Hier ergeben sich jedoch nicht nur Vorteile hinsichtlich der Freiheit in der kreativen Gestaltung, sondern auch im Hinblick auf eine effiziente Materialausnutzung und die sich daraus ergebenden Implikationen auf die Nachhaltigkeit des Produktionsprozesses. Und nicht zuletzt kann die schalungslose Fertigung von Betonbauteilen die Produktionskosten deutlich reduzieren. Dieses Potenzial soll nun durch zeitgemäße Techniken wie den computergesteuerten 3D-Betondruck entwickelt werden.
So war es das erklärte Ziel des Projektes, die bereits seit Langem genutzte Spritzbetontechnologie zu automatisieren und in einen robotergesteuerten „3D-Spritzdruckprozess", der den Namen „Shotcrete 3D Printing“ (SC3DP) trägt, zu überführen. Neben der Entwicklung der gesamten Prozesstechnik war es dabei notwendig, einen geeigneten Spritzbeton zu entwickeln, dessen Eigenschaften auf die jeweiligen Bauteile und den Fertigungsprozess eingestellt werden können. Dabei brachte sich MC sowohl beratend als auch mit der Bereitstellung von geeigneten Betonzusatzmitteln ein.
Die Forschung zum SC3DP findet am „Digital Building Fabrication Laboratory“ (DBFL) der TU Braunschweig, einem digital gesteuerten Fertigungszentrum, welches kooperative Arbeitsvorgänge einer CNC-gesteuerten 5-Achs-Portalfräse und einem integrierten Schwerlastroboter mit insgesamt neun Freiheitsgraden ermöglicht, statt. So können verschiedene robotergestützte Techniken zur Fertigung räumlicher, geometrisch komplexer Betonbauteile eingesetzt werden, wie beispielsweise die Kombination aus Nassspritzverfahren und Fräsarbeiten. Dies ermöglicht das additive und subtraktive Fertigen von Bauteilen und erschließt somit neue Wege, komplexe Bauteile automatisch und effizient aufzubauen.
Erfolgreiches Projekt an der TU Dresden
An der TU Dresden entwickeln Ingenieure und Forscher um Prof. Dr.-Ing. Viktor Mechtcherine seit September 2014 neue Techniken für den 3D-Druck im Extrusionsverfahren. Der Arbeitstitel des ersten Projektes lautete: „Machbarkeitsuntersuchungen zu kontinuierlichen und schalungsfreien Bauverfahren durch 3D-Formung von Frischbeton“. Im Gegensatz zu den bisher bekannten Ansätzen lag in diesem Forschungsvorhaben ein besonderer Fokus auf der praxistauglichen Umsetzung direkt auf der Baustelle (Ortbetonbau). Die anvisierte gerätetechnische Basis besteht daher aus etablierten Baumaschinen und als Baustoffe kommen die im Massivbau üblichen Betone zum Einsatz. Der streng an der gängigen Praxis ausgerichtete Forschungsansatz zeigte Wirkung! Zur Freude der Beteiligten wurde das Konzept im Jahre 2016 durch den Preis der weltweit größten Baumaschinenmesse bauma in München in der Kategorie Forschung ausgezeichnet. Es entwickelte sich im Projektzeitraum ein so stark wachsendes Interesse von Medien und Unternehmen an der innovativen Technologie, dass die TU Dresden zur Sicherung ihrer Forschungsergebnisse ein Markenrecht für das „CONPrint3D® – Concrete on-site 3D Printing“ getaufte Verfahren beim Deutschen Patent- und Markenamt eintragen ließ. Im Zuge des Forschungsprojektes wurden schließlich technische Lösungen für die Betonförderung, den notwendigen Druckkopf und die Großraumrobotik erarbeitet und bewertet. Parallel erfolgte die Entwicklung eigens für den 3D-Druck optimierter Betone sowie die Untersuchung von deren rheologischen bzw. mechanischen Eigenschaften in frischem und erhärtetem Zustand. Zudem wurde die baubetriebliche Prozessoptimierung analysiert. So lieferte der Versuchsaufbau des CONPrint3D® Versuchsstandes neben dem Beweis der technischen Machbarkeit auch wichtige Fakten für die Wirtschaftlichkeitsbetrachtungen des 3D-Betondrucks.
Beim Druck einer kompletten Beispieletage, wie sie in einem Mehrfamilienhaus zu finden sein könnte, erwies sich die Herstellzeit der Wände als 4- bis 6-mal schneller als in konventionellen Bauverfahren. Zudem sind weitere Reduzierungen der Ausführungszeit durch eine Erhöhung der Schichtdicke oder der Betoniergeschwindigkeit denkbar. Darüber hinaus ergaben die Berechnungen: im Vergleich zum Erstellen des gleichen Geschosses in Mauerwerksarbeit eine Kostenersparnis von rund 30%. Dabei blieb der Umstand, dass der Rohbau im Prinzip ohne Gerüste und Hochbaukräne errichtet werden kann, sogar noch unberücksichtigt. Die Entwicklung des neuen Verfahrens wird derzeit weiter im Rahmen eines ZukunftBau-Nachfolgeprojektes vorangetrieben, bei dem der 3D-Druck mit Schaumbeton im Vordergrund steht. Dabei werden Schaumgeneratoren der MC in den Prozessablauf integriert.
MC – Partner der Forschung
Die Forschung hat auch bei der MC im Haus einen hohen Stellenwert. Schließlich verdankt das Unternehmen seinen guten Ruf auch der ständigen Entwicklung bauchemischer Innovationen. Chemiker, Mineralogen und Baustofftechniker der MC arbeiten weltweit eng mit dem technischen Produktmanagement und den Fachberatern aus dem Vertrieb zusammen. Dazu kommen die regelmäßige Mitwirkung bei nationalen und internationalen Forschungsprojekten und die Kooperation mit Universitäten sowie externen Materialprüfanstalten.
Nach umfangreichen Versuchen wurde beim Projekt in Braunschweig für die Betonmischung schließlich ein Betonersatzsystem der MC eingesetzt, das speziell für das Forschungsprojekt entwickelt worden ist und die besten Ergebnisse zeigte. Auch beim Forschungsprojekt In Dresden griff man gern auf das Know-how der MC-Experten zurück. Dabei wurden nach umfangreichen Vorversuchen und Funktionstests mit dem begleitendem Personal in den MC-eigenen Labors in Bottrop schließlich Betonzusatzmittel inklusive modifizierter Beschleunigungssysteme geliefert. Neben der beratenden Begleitung des Forschungsvorhabens war die Einschätzung der Experten der MC auch bei der Beurteilung der Verwertungschancen der entwickelten Technologien am Weltmarkt gefragt.
Zukunftstechnik mit Perspektive
Steht diese Technologie auch noch am Anfang, so hat sie doch bereits ihre Praxistauglichkeit international mehrfach unter Beweis gestellt. Im Mai 2016 wurde in Dubai das erste vollständig gedruckte Bürogebäude der Welt eröffnet. Die Vereinigten Arabischen Emirate verfolgen sogar eine staatlich geförderte „3D-Printing Strategy“ – mit dem Ziel, bis 2030 ein Viertel aller Neubauten im Golfstaat mittels 3D-Druck herzustellen. Auch das chinesische Unternehmen „Win Sun“ verwendet bereits einen industriell einsetzbaren Beton-3D-Druck, bei dem die Einzelteile standardisierter Wohnhäuser in einer Fabrik gedruckt und später auf der Baustelle nur noch zusammengefügt werden müssen.
Ganz aktuell ist ein Projekt aus Mailand: Ein etwa 100 Quadratmeter großes, eingeschossiges Demonstrationsgebäude wurde konstruktiv aus 35 modularen Elementen, die ein Roboter hergestellt hat, aufgebaut. Der flexible Drucker benötigte für den 3D-Druck der einzelnen Elemente jeweils 60 bis 90 Minuten. Die effektive Bauzeit für das komplette Gebäude betrug damit lediglich 48 Stunden. So ist der 3D-Betondruck auf dem besten Wege, ein wichtiger Baustein in der Bauwelt zu werden.
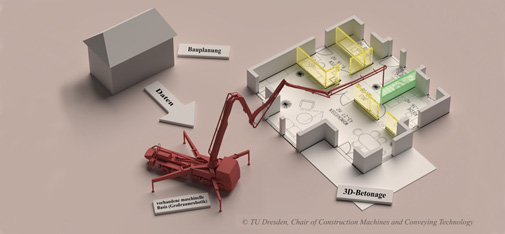
© Professur f. Baumaschinen, TU Dresden
ÄHNLICHE INHALTE
-
News
Klicken Sie hier, um zu unseren News zu gelangen.
-
MC-Pedia
In unserer MC-Pedia finden Sie fachliche Artikel zu unterschiedlichen Themen, die exklusiv von unseren Spezialisten geschrieben wurden.
-
Magazine
Klicken Sie hier, um zu den aktuellen Ausgaben unseres Kunden- und Mitarbeitermagazins MC aktiv zu gelangen.
-
Downloads
Hier finden Sie alle relevanten Datenblätter unserer Produkte sowie Broschüren unseres Unternehmens sowie unserer Fachgebiete und Produktkategorien.
-
Referenzen
Klicken Sie hier, um zu unseren aktuellen Referenzen und Projektberichten zu gelangen.
-
Karriere
Klicken Sie hier, um zum MC-Karrierebereich zu gelangen.
-
Kontakt
Klicken Sie hier, um zu unserer Kontaktseite zu gelangen.